Home » Screws
Screws
Plasticizing screws are fundamental in plastic processing, ensuring the correct melting and mixing of the material. Their carefully designed profile directly affects the performance and quality of the production process, optimizing material flow and reducing waste.
The use of special steels and surface treatments improves durability and performance, ensuring a long service life even under harsh working conditions and when processing corrosive materials.
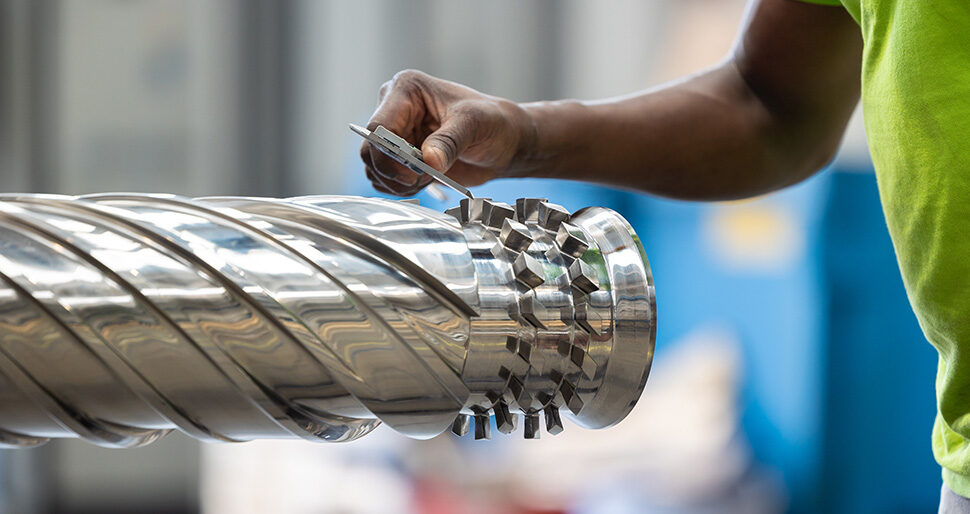
Screw profile
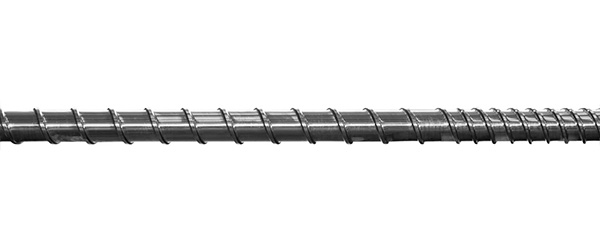
Pitch and profile of the screw
The pitch of the screw determines the distance between two screw flights and is crucial for controlling the feed rate of the plastic material and its movement along the screw. The shape and profile of the screw are designed to promote mixing, homogenization, and uniform heating of the plastic material during the plastification process.
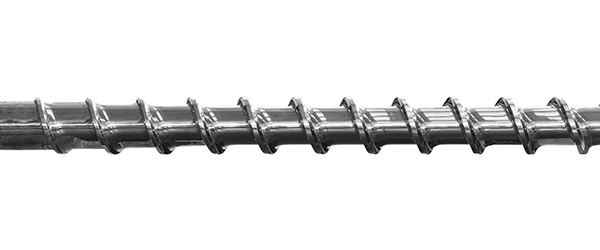
Channel depth
Channel depth in a screw refers to the distance from the root of the screw (the bottom of the channel) to the tip of the flights (the top of the channel). This parameter affects the plastic material’s mixing capability and the plastification pressure in the process. The core taper refers to the gradual reduction in the diameter of the core (the interior of the screw) along the length of the screw. This design helps to control the heating and mixing of the plastic material during the plastification process.
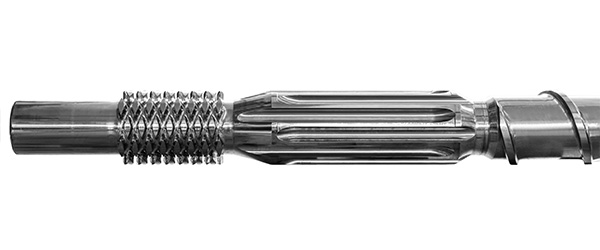
Mixer
The mixer is a section designed to ensure homogeneous mixing of plastic materials and additives during the plastification process, thereby enhancing the quality of the final product. Its configuration and operation are crucial for controlling the mixing, homogenization, and even distribution of components within the plastic material before extrusion.
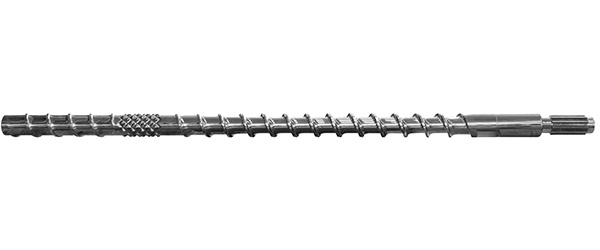
Length of the feed, transition and meter zones
Feed, transition and meter zone sare designed to control the movement and behavior of the plastic material along the screw during the plastification process. The length and profile of these zones affect temperature distribution, material melting, and plastification pressure.
Materials
The steel alloys used to make screws for use in plastics processing machines are nitriding steels, hardening steels and also stainless steels. Below are some of the most commonly used alloys:
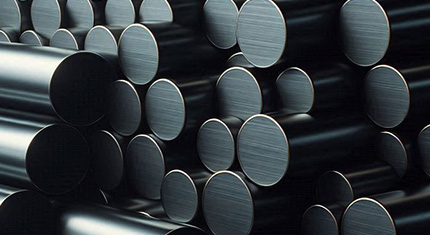
41CrAlMo7 steel - Material 1.8509
41CrAlMo7 is a chromium-molybdenum steel alloy used in high-temperature applications, including plasticizing screws for extruders. Its mechanical properties, such as strength and hardness, along with its resistance to high temperatures, make it suitable for extreme working environments like those found in resin plasticization extruders. This steel also offers good wear and abrasion resistance, contributing to the durability and performance of plasticizing screws.
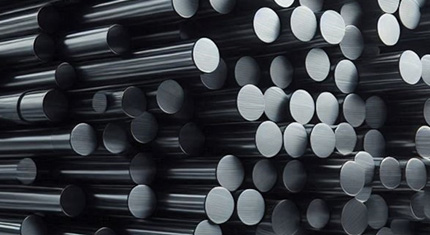
34CrAlNi7 steel - Material 1.8550
34CrAlNi7 is a chromium-aluminum-nickel steel alloy known for its high resistance to corrosion and oxidation at elevated temperatures. This makes it suitable for applications in high-temperature environments and aggressive atmospheres, such as plasticizing screws used in the plastic processing industry. The alloy provides a combination of mechanical strength, toughness, and high-temperature resistance, enhancing the durability and performance of plasticizing screws under severe operating conditions.
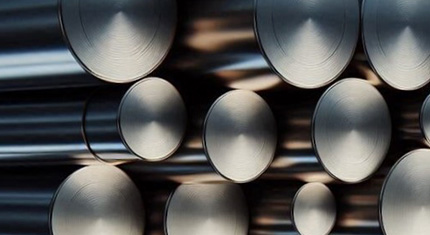
31CrMoV9 steel - Material 1.8519
31CrMoV9 steel is a special alloy that combines mechanical strength and hardness, used in industrial and advanced mechanical applications. Thanks to the combination of strength and toughness, this steel is used in highly stressed mechanical components. It is moderately difficult to machine, but thanks to its high strength and hardness, it is suitable for the production of critical components that require high mechanical performance. 31CrMoV9 is particularly appreciated for its high fatigue resistance and the ability to maintain properties even in high-temperature environments.
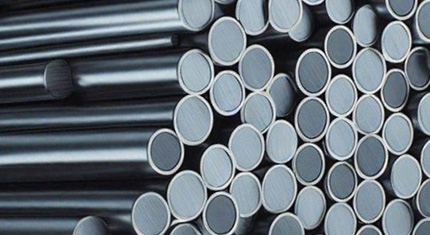
K110 steel - Material 1.2379
K110, also known as AISI D2, is a tool steel alloy renowned for its high wear and abrasion resistance. It is commonly used in the manufacture of plasticizing screw tips and other extruder components that require high wear resistance, hardness, and toughness. Its chemical composition includes carbon (C), chromium (Cr), molybdenum (Mo), vanadium (V), and other elements that contribute to its excellent mechanical properties. K110 steel is particularly valued for its ability to maintain good hardness even at high temperatures, ensuring long-lasting performance in demanding work environments.
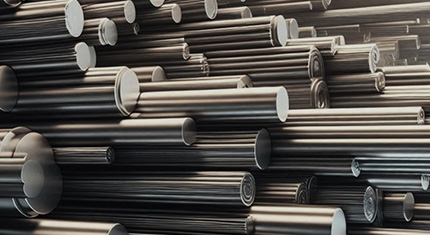
AISI 420 steel
AISI 420 is a martensitic stainless steel alloy with good corrosion resistance, wear resistance, and plastic deformation resistance. It is commonly used in the production of plasticizing screw components and other extruder parts. Its mechanical properties, including hardness, strength, and machinability, make it suitable for applications requiring a combination of mechanical strength and corrosion resistance. AISI 420 is also known for its ability to be hardened and tempered to achieve optimal hardness, making it a popular choice for a wide range of industrial applications.
Treatments
Ion nitriding
Use of ionized nitrogen gas (such as atomic nitrogen or molecular nitrogen) in a vacuum chamber
Gas nitriding
Exposure of the metallic material to a nitrogen-rich gas mixture at high temperatures
Hardening
Heating the metallic material to a high critical temperature and then rapid cooling
Coating
To increase the resistance of the screw crests to abrasion, hard metal coatings are made, with different chemical compositions depending on the result you want to obtain: greater hardness may correspond to less resistance to impacts, so you need to know what you need and which solutions to choose. The material the cylinder is made of also affects the choice of reinforcement of the screw crests: a bimetal cylinder allows you to use screws with particularly hard reinforcements, while with a nitrided cylinder you will have to use softer alloys to reinforce the screw crest, to avoid the risk of the screw “digging” into the inside of the plasticizing chamber.
Here following some examples of hardfacing solution, for other requirements pease contact us.
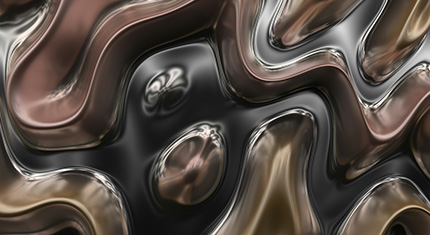
Stellite gr 12
Base: Cobalt
Elements: C – Cr – W
Hardness: 44 – 48 HRC
Abrasion resistance: ●●●
Corrosion resistance: ●●●
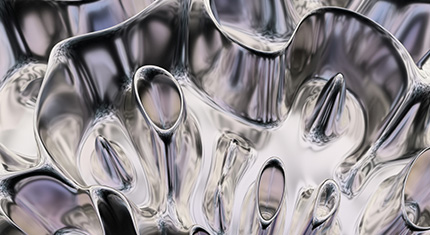
Colmonoy 56
Base: Nickel
Elements: C – Si – Cr – B – Fe
Hardness: 52 – 56 HRC”
Abrasion resistance: ●●●
Corrosion resistance: ●●●
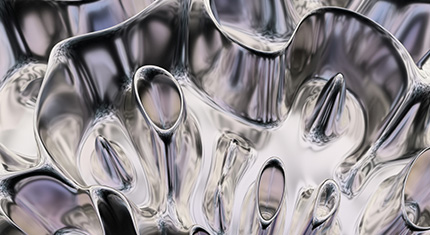
Colmonoy 83
Base: Nickel
Elements: C – Si – Cr – B – Fe
Hardness: 56 – 60 HRC”
Abrasion resistance: ●●●●●
Corrosion resistance: ●●●●●
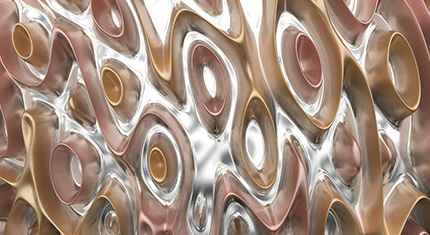
Casto TIG 5
Base: Iron
Elements: Cr – V
Hardness: 58 – 62 HRC
Abrasion resistance: ●●●●
Corrosion resistance: ●●