I KPI (Key Performance Indicators) sono indicatori chiave di prestazione utilizzati per misurare l’efficienza, la produttività e il successo di specifici processi o attività. Importanti KPI legati alla produzione industriale sono ad esempio:
- Efficienza operativa (OEE).
- Tasso di difetti (Defect Rate).
- Tempo di inattività (Downtime).
- Produzione per ora (Units Per Hour).
- Utilizzo delle risorse (Resource Utilization).
Proviamo a vedere insieme il primo.
L’indice di efficienza di un macchinario, spesso chiamato anche rendimento o efficienza operativa, misura quanto efficacemente un macchinario utilizza l’energia o le risorse disponibili per produrre un risultato utile. Questo indice è una metrica fondamentale per valutare le prestazioni dei macchinari industriali e la loro economicità.
Mentre il rendimento energetico è pari al rapporto tra energia immessa o utilizzata ed energia prelevata, ed è quindi sostanzialmente una misura di quanta energia un elemento disperde, l’indice di Efficienza Generale è ben più utile in un contesto aziendale produttivo e guardando ad un macchinario nel suo insieme.
OEE (Overall Equipment Effectiveness)
Nell’industria manifatturiera, un indicatore complesso come l’OEE viene spesso utilizzato per valutare le performance generali del macchinario. L’OEE considera tre fattori principali:
- Disponibilità (tempo di operatività rispetto al tempo totale disponibile)
- Prestazione (velocità di produzione effettiva rispetto a quella ideale)
- Qualità (prodotti senza difetti rispetto al totale)
La formula per l’OEE è: OEE = Disponibilità x Prestazione x Qualità
dove ogni parametro è espresso come percentuale. L’OEE complessivo dà un’indicazione del rendimento del macchinario rispetto al suo potenziale massimo.
Esempio pratico di calcolo se calcoliamo l’OEE, per esempio con:
- Disponibilità: 90%
- Prestazione: 95%
- Qualità: 98%
Avremo:
OEE = 0.90 x 0.95 x 0.98 = 0.8361 ovvero 83.61%
Perché è importante l’indice di efficienza?
Al di là dei numeri e delle formule matematiche, è evidente che un alto indice di efficienza indica che il macchinario utilizza bene le risorse disponibili, con meno sprechi energetici e materiali, e migliorando la sostenibilità e riducendo costi operativi dell’azienda.
Nel calcolo, è abbastanza chiaro cosa sia la qualità: è il rapporto tra pezzi buoni e pezzi totali prodotti. Se la macchina lavora sempre (massima disponibilità) e al massimo ritmo possibile, ma produce un’elevata quantità di scarti, è ovvio che l’efficienza sarà bassissima.
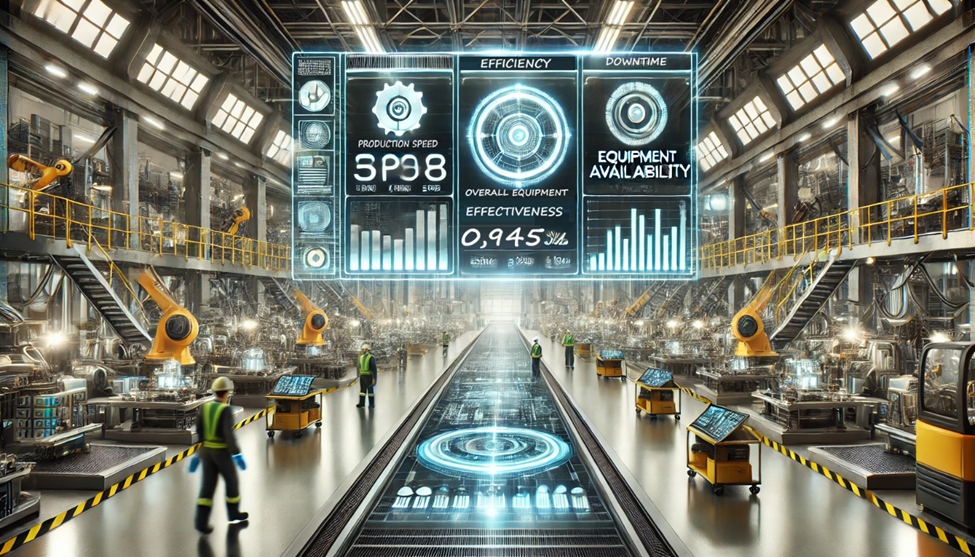
Cosa vuol dire invece, e come si calcola, la disponibilità macchina?
L’indice di disponibilità macchina, in un contesto di produzione industriale, è una misura delle prestazioni di un’apparecchiatura o di una macchina rispetto alla sua capacità di essere operativa e produttiva. Viene calcolato per monitorare quanto tempo una macchina è effettivamente disponibile per produrre, rispetto al tempo totale in cui è richiesta per la produzione.
In altre parole, quante più ore di fermi macchina non previsti e non programmati si verificano, tanto più bassa sarà la disponibilità.
Attenzione: le manutenzioni programmate, i fermi per attrezzaggio, pulizia, i tempi di accensione e spegnimento, non incidono sull’indice di disponibilità macchina, proprio perché è noto a priori (quindi un onere preventivabile e calcolabile) il tempo necessario per queste operazioni, durante le quali la macchina non può essere produttiva.
Lo si capisce anche dalla formula di calcolo dell’indice di disponibilità (D) che è infatti calcolato come:
D =(Tempo di funzionamento effettivo \ Tempo totale programmato) x 100
Dove:
- Tempo di funzionamento effettivo: il tempo durante il quale la macchina è stata operativa e ha effettivamente prodotto beni.
- Tempo totale programmato: il tempo totale durante il quale la macchina era programmata per essere operativa, esclusi i periodi di fermo programmato come manutenzioni pianificate.
Interpretazione dell’Indice di Disponibilità
Un indice di disponibilità del 100% indica che la macchina è stata disponibile per l’intero tempo previsto, senza guasti o interruzioni impreviste. Valori inferiori indicano una presenza di fermi macchina non programmati, suggerendo possibili aree di miglioramento nella manutenzione, nella gestione degli imprevisti o nell’ottimizzazione dei tempi di fermo.
Utilità dell’Indice di Disponibilità
L’indice di disponibilità è dunque uno dei tre indicatori principali dell’OEE (Overall Equipment Effectiveness), che si utilizza per valutare l’efficienza complessiva di una macchina. Monitorare questo indice aiuta le aziende a individuare problemi di affidabilità e a prendere decisioni per migliorare la produttività e la continuità delle operazioni.
Per aumentare la disponibilità macchina bisogna:
- Programmare le manutenzioni, effettuarle preventivamente potendole pianificare nei tempi più adatti (ad esempio programmando contemporaneamente la presenza o l’assenza di determinato personale – operatori di produzione o manutentori); preparare le risorse e i ricambi per tempo pronti e disponibili permette di effettuare riparazioni (ed anche upgrades) in tempi certi e più ridotti rispetto ad interventi di riparazione di emergenza.
- Pianificare a intervalli regolari il controllo dello stato di usura dei componenti chiave del macchinario è uno dei metodi fondamentali per anticipare le criticità, il che significa evitarle. Viti e cilindri di plastificazione consumati, oltre a essere un rischio per la disponibilità macchina, incidono anche su un altro dei parametri dell’efficienza globale del macchinario: la qualità del prodotto. Un gruppo di plastificazione usurato può portare, oltre chiaramente a perdita di volumi, a cattiva miscelazione dei materiali, bruciature, aumento dei consumi energetici.
E voi, siete sicuri che risparmiare sui ricambi, e correre a cercare una soluzione all’ultimo momento, con la linea in funzione, accontentandosi di ciò che si trova velocemente e disponibile anche se non è esattamente la vite, il profilo, il trattamento che serve, sia così conveniente?