Key Performance Indicators (KPIs) are key metrics used to measure the efficiency, productivity, and success of specific processes or activities.
Important KPIs in industrial production include:
- Operational Effectiveness (OEE)
- Defect Rate
- Downtime
- Units Produced Per Hour
- Resource Utilization
Let’s take a closer look at the first indicator.
Operational Effectiveness of Machines (OEE)
The efficiency index of a machine, often referred to as operational effectiveness or efficiency, measures how effectively a machine uses the available energy or resources to achieve a useful output. This index is a key metric for evaluating the performance and cost-effectiveness of industrial machines.
While energy efficiency represents the ratio of energy used effectively to the energy consumed (essentially measuring how much energy a system wastes), the Overall Equipment Effectiveness (OEE) is far more useful in a productive industrial setting, particularly when considering a machine as a whole.
OEE (Overall Equipment Effectiveness)
In the manufacturing industry, a complex indicator like OEE is often used to evaluate a machine’s overall performance. OEE considers three main factors:
- Availability: Operating time relative to the total planned time.
- Performance: Actual production speed compared to the ideal speed.
- Quality: Defect-free products as a proportion of total production.
The formula for OEE is:
OEE = Availability × Performance × Quality,
where each parameter is expressed as a percentage. The overall OEE value indicates how efficiently a machine operates compared to its maximum potential.
Example Calculation:
Assume we calculate the OEE with the following values:
- Availability: 90%
- Performance: 95%
- Quality: 98%
The calculation is:
OEE = 0.90 × 0.95 × 0.98 = 0.8361 or 83.61%.
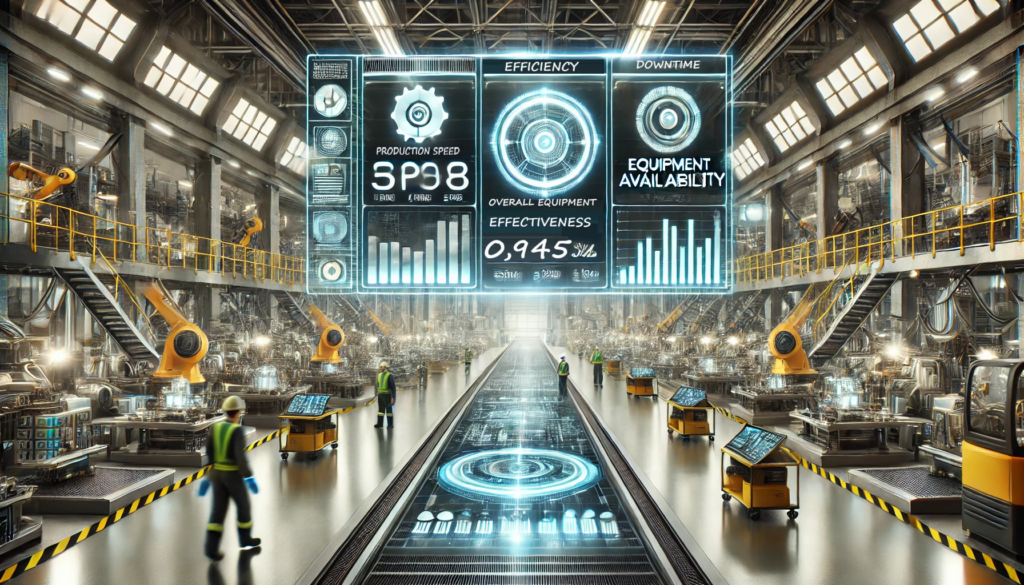
Why is the Efficiency Index Important?
Beyond the numbers and mathematical formulas, a high efficiency index demonstrates that a machine is effectively utilizing resources, wasting less energy and material, improving sustainability, and lowering the company’s operational costs.
In the calculation, quality is relatively straightforward: it represents the ratio of good parts to total parts produced. However, even if a machine runs continuously (maximum availability) and operates at maximum speed, its efficiency will be very low if it has a high defect rate.
What Does Machine Availability Mean and How Is It Calculated?
The availability index of a machine measures, in an industrial production context, the device’s or machine’s ability to be operational and productive. This index is calculated to monitor how much time a machine is actually available for production compared to the total time it is needed for production.
The more unplanned and unforeseen downtimes occur, the lower the availability.
Note: Planned maintenance, changeovers, cleaning, and start-up or shutdown times do not affect the availability index because the required time is known in advance and can be accounted for.
The formula for the availability index (A) is:
A = (Actual Operating Time ÷ Planned Total Time) × 100
Where:
- Actual Operating Time: The time during which the machine was operational and actively producing.
- Planned Total Time: The time the machine is scheduled to be operational, excluding planned downtimes like maintenance.
Interpretation of the Availability Index
An availability index of 100% indicates that the machine was available throughout the entire planned time without any disruptions or unplanned interruptions. Lower values suggest unplanned downtimes, which indicate potential areas for improvement in maintenance, handling unforeseen issues, or optimizing downtimes.
Usefulness of the Availability Index
The availability index is one of the three main components of OEE (Overall Equipment Effectiveness) and is used to evaluate the overall efficiency of a machine. Monitoring this index helps businesses identify reliability issues and make decisions to improve productivity and continuity of operations.
How to Increase Machine Availability
- Plan and Perform Preventive Maintenance:
Planned maintenance should be carried out on time, ideally considering the availability of personnel (e.g., production or maintenance staff). Pre-prepared resources and spare parts allow for faster and better-predictable repairs compared to emergency repairs. - Regular Wear Monitoring:
Checking the wear of key components is critical to anticipating and avoiding potential problems. Worn-out screws and cylinders not only pose a risk to availability but also negatively affect product quality – another key parameter for the machine’s overall efficiency.
A worn-out plasticizing unit can lead to volumetric losses, poor material mixing, burns, and increased energy consumption.
Is It Really Worth Skimping on Spare Parts?
Is it worth waiting until the last minute to look for a solution while the production line is running, settling for whatever is quickly available, even if it’s not exactly the screw, profile, or surface treatment required?