Among the most common requests Viplas receives from customers is, unsurprisingly, how to extend the “lifespan of screws.” Like any mechanical part, the plasticizing screw (and barrel) is subject to wear. Additionally, depending on the type of polymers processed, the presence or absence of chemical or mineral additives, the pressures, and temperatures that develop inside a plasticizing group, significant corrosion and abrasion can occur. The first signs usually appear on the screw crest, but in progressively more severe cases, they can also impact the flanks of the profile and the core.
In many cases, it’s possible to restore the original dimensions (or at least functional ones) of the screw (and the barrel interior) through precise reconditioning, and Viplas specializes in this. However, sometimes the damage is so extensive or deep that the screw becomes pitted, full of craters, and/or the helix almost disappears.
So, how can we prevent wear, corrosion, and abrasion? How can we make a more durable screw when “simple” thermal treatments (such as hard tempering or nitriding) and surface treatments (such as chrome plating) are insufficient?
A lesser-known but highly valuable solution that Viplas offers is PVD coatings. PVD (Physical Vapor Deposition) surface treatment is an advanced coating technology that enhances the surface properties of metals. It involves the physical deposition of a thin layer of material onto a metal substrate through the vaporization and condensation of material in a vacuum. This technique is commonly used to increase surface hardness, wear resistance, corrosion resistance, and, in some cases, improve aesthetics.
Which treatment to use for plasticizing screws?
The choice of PVD treatment for screws depends on the specific application and required properties. For example, in applications that demand high wear and corrosion resistance in aggressive environments, chromium nitrides (with an optional oxidized layer on top), known as CrN or CrON, may be more suitable.
Factors to consider when selecting the most appropriate PVD treatment include:
- Type of plastic: Different plastics have varying adhesive, abrasive, and/or corrosive properties. For instance, the chlorine vapors produced in the plasticizing chamber when processing PVC can corrode the screw and barrel.
- Presence of fillers: Fillers in plastic can impact the material’s abrasiveness. For example, processing materials loaded with fiberglass or calcium carbonate necessitates specific protective measures.
Specific advantages for screws:
- Reduced friction and wear: PVD coatings, such as TiN (titanium nitride) and CrN (chromium nitride), create an extremely smooth and hard surface, significantly reducing friction between the screw and the barrel. This directly translates to longer service life, as reduced wear extends the lifespan of the screw and barrel, lowering replacement frequency and maintenance costs.
- Corrosion resistance: Exposure to aggressive chemicals and high temperatures can cause screw corrosion. PVD coatings provide excellent protection against corrosion, preserving the component’s integrity.
- Prevention of plastic adhesion: The anti-adhesive properties of PVD coatings significantly reduce plastic adhesion to the screw surface, preventing build-up and ensuring better final product quality. Some coatings offer a smoother surface finish than others, which can enhance “Anti-Sticking” properties, minimizing the likelihood of processed material sticking to the screw. This is a common requirement for rubber processing.
- Improved heat dispersion: Some PVD coatings also exhibit high thermal conductivity, aiding in better heat dissipation generated by the friction of molten plastic.
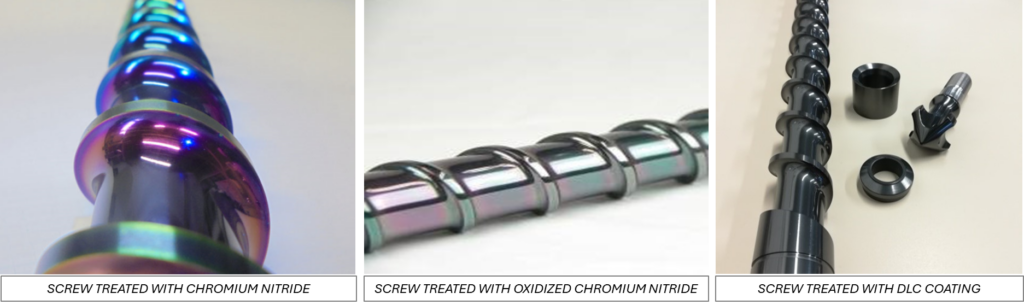
Key points to keep in mind when considering a PVD coating:
- Surface preparation: Proper surface preparation of the screw is essential for ensuring good coating adhesion. For example, the screw must be free from residues, such as the white dust typical of nitriding. Therefore, some PVD treatments require screw polishing beforehand.
- Coating thickness: Coating thickness affects the final properties. Thicker layers generally improve wear and corrosion resistance but may increase costs. However, it’s worth noting that the thickness of PVD-deposited treatments is very thin, so there’s no need to account for it when machining screws; the treatment thickness won’t affect screw dimensions beyond tolerance.
- Process control: Careful monitoring of the PVD deposition process is essential to ensure coating quality and uniformity. Companies specializing in these treatments often design and build their equipment for precise control.
- Treatment cost: These treatments do make screws significantly more expensive, and different solutions come with varying costs. Among them, DLC (diamond-like carbon) treatment is extremely effective but also the most expensive. Therefore, a thorough analysis of customer requirements, process characteristics, and the cost/benefit balance is crucial.
In conclusion
PVD treatments offer numerous advantages for screws used in injection molding and extrusion equipment. Choosing the most suitable treatment requires a careful evaluation of operating conditions and specific application requirements. Viplas is available to discuss your specific needs and recommend a solution that best aligns with your performance and cost expectations. We can also arrange special trial conditions for screws to help identify the best solution at an appropriate cost together.