Home ยป Tips
Tips
Screw tips are an essential part of the plasticizing units.
In the injection molding process, the seal between the ring, valve, and feed material is the key to success. A hermetic seal prevents material from leaking out of the injection chamber, ensuring a controlled and uniform flow towards the mold.
Positioned at the end of the screw, they serve several crucial functions. They regulate the flow of plastic material during plasticization and must close securely to avoid leaks or undesired flows. They ensure uniformity in material dosing, thereby guaranteeing consistent quality of the produced parts and high repeatability in the production process.
They must be made from wear-resistant and high-temperature-resistant materials to ensure prolonged durability and reliable performance over time. We can supply nozzles with special heat treatments, in sintered steel (recommended when extreme resistance, including corrosion resistance, is required), with hard metal coatings on the base of the fins.
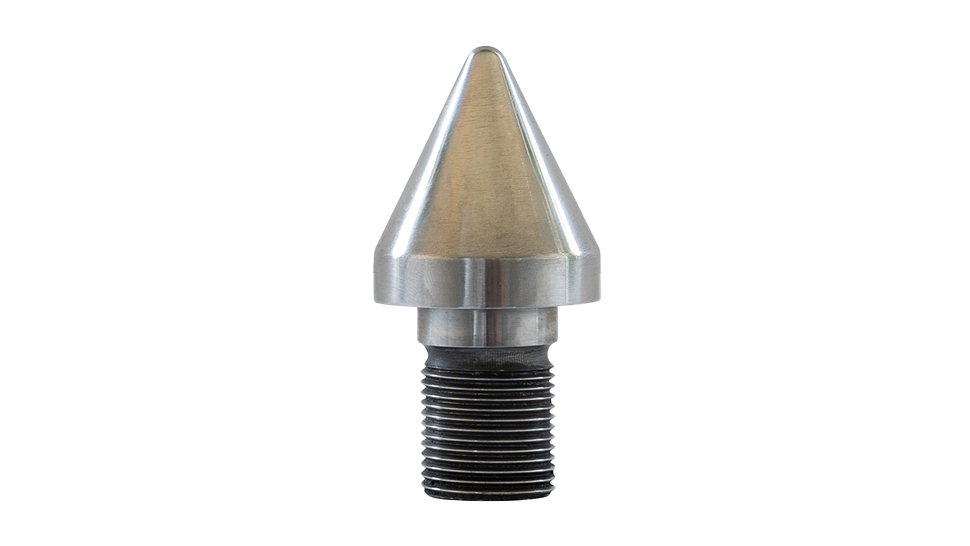
Extruder tips
In extrusion screws, the tip can be either machined directly onto the screw body (fixed and integral) or removable.
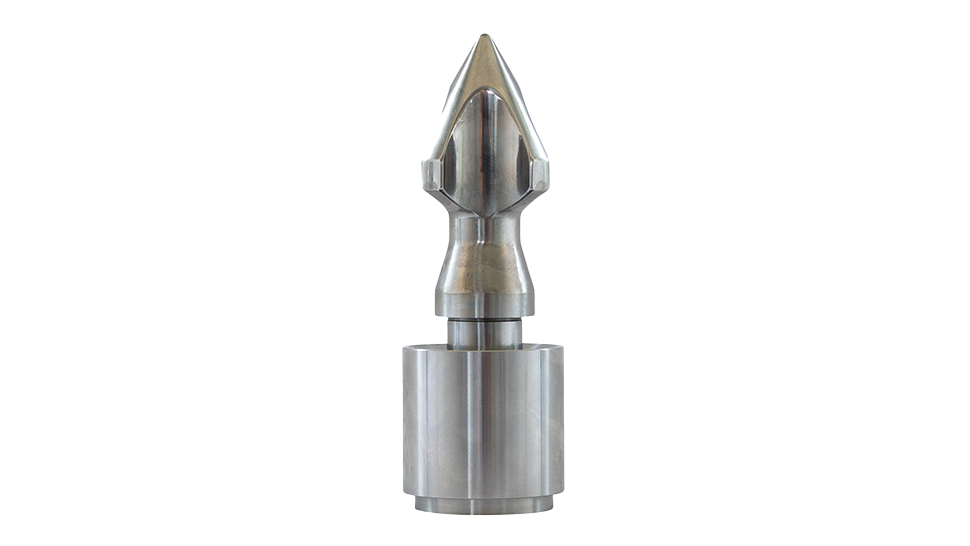
Valve-flange tips
They represent the most commonly used and simplest solution, where the axial movement of the screw translates into the closure of the valve on the flange, thereby blocking the flow of molten material. The simple three-part construction allows for replacing only the worn components.
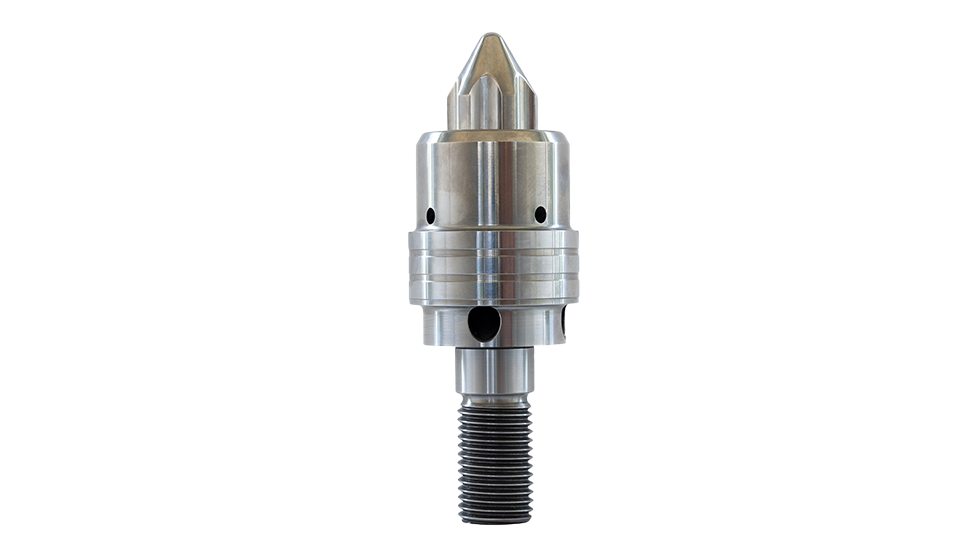
Special tips: ball valve, spiral hole, mixing
In ball tips, the flow of plastic material is controlled by a movable ball inside the injection channel. They are known for their reliability and long-lasting performance.
Tips with a spiral hole design help to improve the mixing and homogeneity of the plastic material during injection.